When I went to bed last night I was anticipating spending a Sunday afternoon working on my new Lithium Iron Phosphate (LFP) battery system for Sun King, the solar-powered expedition launch. It didn’t work out that way.
I woke up knowing something wasn’t right and it evolved to the realization that I was sick and was going nowhere. It’s one of those weird ones, so I am trying to ride it out and figure out what I can do from my bed. If I can’t build a battery I can muse about it, surely.
Yesterday evening I went out and puttered, verifying that 4 cell blocks (12v) will fit in a standard group 24 battery box. This morning I ordered some more boxes only as I did not have 4 of them. One is in use and the one didn’t look too good after the tractor ran over it. BAD TRACTOR!
Now I can plot and plan. Yes, it looks like there is room in the boat’s battery cabinet for two of the plastic boxes. Height should be good, too. I will bring the boat to the Solar Shed to start fitting.
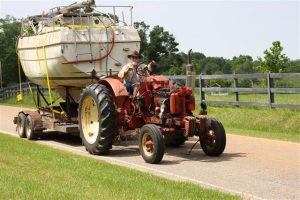
One of the things to accommodate is the BMS or battery management system controller. In this case, I have Daly 8s units. The 8s refers to how many cells it supports. 8 (X3v/cell) is what you use for a 24 volt battery, which I use on Sun King. This one is also made for LFP cells as opposed to LI or Lithium Ion cells. They are just enough different you have to have the right one. Beyond the cell capacity, this one has a current capacity of 100 amps for charging and 200 amps for discharge. There are bigger ones and smaller ones. The boat cruises at 25 amps, but the 5kw inverter that powers the galley will pull 40 or 50 amps when brewing coffee or nuking some food. Charging with 810 watts won’t stress anything. These units are what Courtney had handy, but they will be great for the Sun King. If I migrate these cells later to the Solar Yacht project, I will just put both of the current battery cell groups in series and change to a S16 BMS.

When the cells were first imported they were well balanced from CATL, the maker. Balanced cells are important. These have been unused for about a year, so Courtney balanced them again before bringing. This involved bolting them all in parallel and then charging to 3.65 volts. Never go higher. Once they are all in series, we will set the upper limit to the equivalent of 90% charge to make the cells last longer. This will be done either with the charge controller or the BMS or both. I have not yet fired up the BMS to determine what features it has. The documentation is what I call “lacking.” That’s being charitable. Yet, people use these things every day and all is well.
A block of 4 cells is connected in series with bus bars, which are metal bars with holes to slip over the terminals. I don’t know where the “bus” thing came about, but it has been around longer than lithium batteries. A cable will go from one block to the next between the plastic boxes. That gives us a 24 v battery (Actually 25 and change.) This would work as is if you want to go out in the boat to power your trolling motor. However, at some point you have to charge it and this is where the BMS is important.
The models and brands vary a little bit, but in our case we have a fat blue wire coming out of the BMS and that connects to the negative terminal of the battery. The fat black wire becomes your battery system’s negative terminal. The positive terminal at the other end of the battery is the system positive. We are not yet done, though!
This model is equipped with a balancer circuit. This takes a sample of each cell, probably stored in a capacitor, and places it across the next cell. Every cell gets sampled against every other continuously and they all end up and stay the same voltage. This makes them last longer. You can do the same with lead acid batteries when you have access to individual cells. On my AGM battery bank I have balancers on each battery block. It isn’t as good as having each cell balanced, but it helps.
There is a connector and a provided cable to connect to all the cells. The cable will have to be extended to get to the second cell block and I will probably do that with a 4 pin plug to make disconnection or service easier. An ordinary trailer plug should work. For each cell, I will solder on a ring terminal.
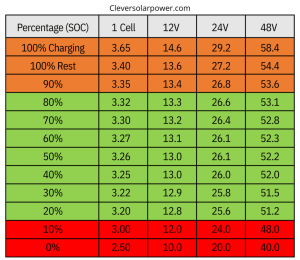
There are other plugins, too. One is a battery meter. It won’t show well through a plywood cabinet, but where there is a will there is a way. The other two gadgets are for communications. There is a Bluetooth dongle for a phone app and a USB adapter for the laptop program. Courtney reports the Bluetooth is no good if the battery is in a metal cabinet, but I think it should work through plywood. Bluetooth has a very short range, so at present I am not certain I can monitor the battery from the captain’s chair. The charge controller and the motor control panels both have meters in them, so there should be no issue in keeping up with things in normal operation. At the end of the day, I go forward to the galley where the batteries are, so the phone app should be useful for checking the day’s statistics, or whatever the heck the app can do! Once the battery system is complete, I need to fire up the app and set all my limits and parmeters. Then we should be ready to connect to the boat.
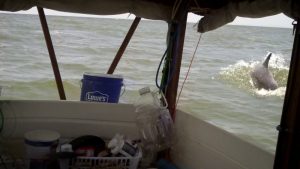
The other connections should be easy. There are already fat cables and circuit breakers in place. The last trick will be to program the charge controller to our maximum voltage setting. According to a chart I found online, a maximum of 90% will be 26.6v.
To be continued….
–Neal
I have enjoyed your post for years. Saw you were doing a boat and lifepo4 batteries.
II found marinehowto.com on lithiums batteries informative and would recommend you read. Specificaly the section on lithium batteries.
Thank you very much for informative blogs and writing over years.